The Role of an Injection Mold Factory in Modern Manufacturing
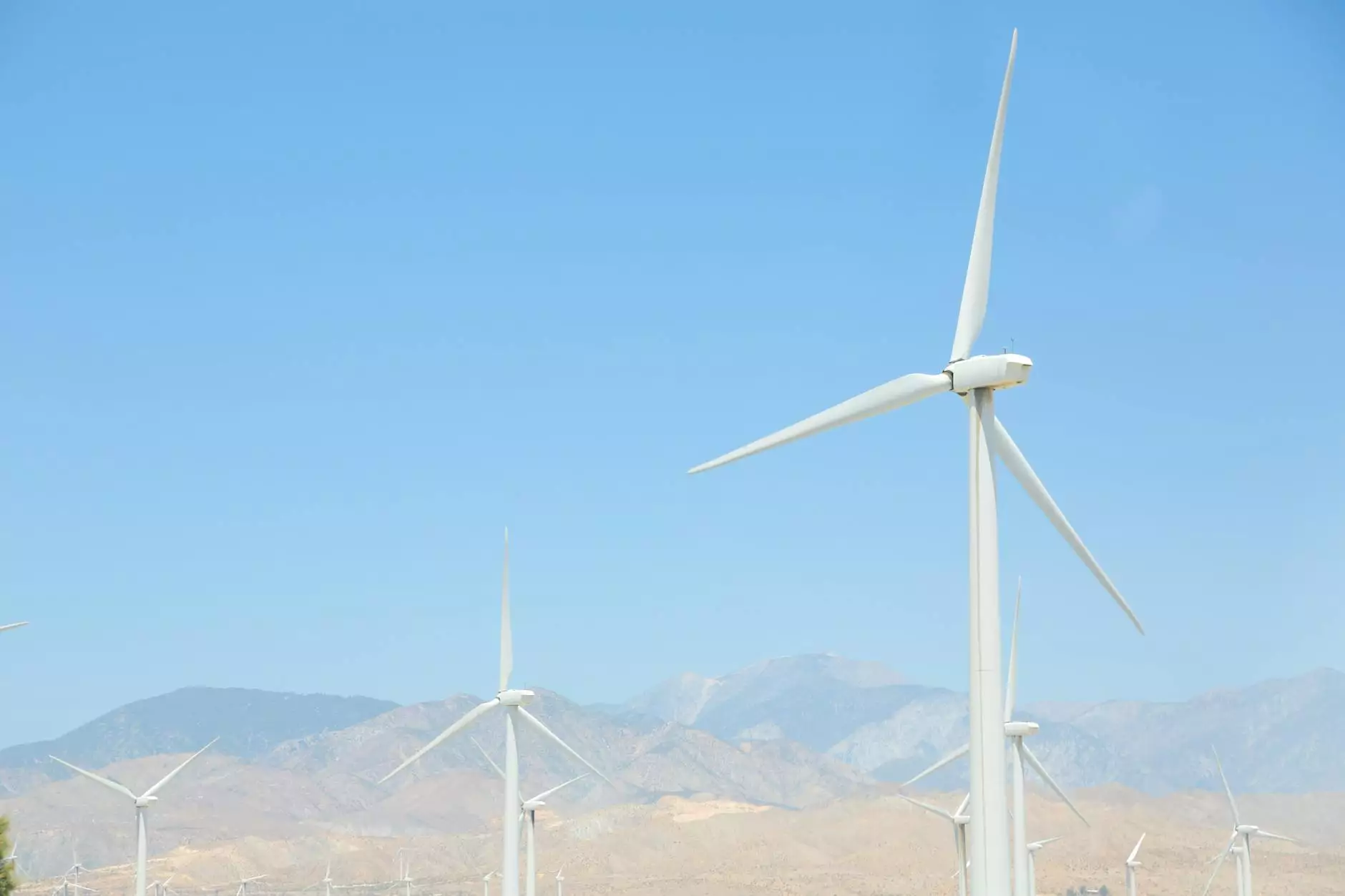
In today's fast-paced industrial landscape, injection mold factories play an essential role in the production of a vast array of products. This article delves into the intricate world of injection molding, exploring the advantages it offers to manufacturers and how it elevates the standards of product quality.
What is Injection Molding?
Injection molding is a manufacturing process used to produce parts by injecting molten material into a mold. The materials commonly used in this process include plastics, metals, and glass. An injection mold factory specializes in this technique and often serves a variety of industries, including automotive, consumer goods, electronics, and medical devices.
Key Advantages of Injection Molding
- High Efficiency: Once a mold is created, a factory can produce thousands of identical parts quickly, making it a highly efficient manufacturing option.
- Precision and Accuracy: Injection molding allows for incredibly precise manufacturing, which means parts fit together seamlessly, reducing the need for additional finishing work.
- Material Variety: The process supports a wide range of materials, providing manufacturers with flexibility in design and functionality.
- Cost-Effectiveness: While the initial investment for creating molds can be significant, the long-term savings in mass production often outweigh these costs.
- Reduced Waste: Injection molding generates minimal waste as the materials can be reused or recycled, making it an environmentally friendly option.
Process of Injection Molding in a Factory
The process followed in an injection mold factory consists of several crucial steps:
- Designing the Mold: Engineers create a detailed design of the mold based on the specifications of the product. This step is critical as it dictates the quality and precision of the final product.
- Creating the Mold: Molds are typically made from steel or aluminum and require high-quality machining to ensure they are accurate and durable.
- Injection: The raw material, usually in pellet form, is heated until it melts and is then injected into the mold under high pressure.
- Cooling: Once the mold is filled, it is cooled to allow the material to solidify and take the shape of the mold.
- Demolding: After cooling, the mold is opened, and the finished part is ejected. This process can be automated for speed and consistency.
- Quality Control: The final parts are inspected for defects and quality assurance to ensure they meet the required standards before delivery.
The Importance of Technical Expertise
A successful injection mold factory requires a blend of technical expertise and innovative technology. Skilled engineers and technicians are crucial in optimizing the injection molding process. Their knowledge ensures that the molds are designed efficiently and that the production process runs smoothly. Continuous training and staying abreast of the latest technological advancements are vital for maintaining a competitive edge in the industry.
Applications of Injection Molded Products
Injection molding finds application across various sectors, producing a multitude of products:
1. Automotive Industry
The automotive industry heavily relies on injection molding for components such as:
- Dashboard panels
- Exterior trim
- Interior parts
- Engine components
2. Consumer Goods
For consumer products, an injection mold factory produces:
- Bottles
- Containers
- Toys
- Household appliances
3. Medical Devices
Injection molding is utilized for medical devices due to the high standards of precision and hygiene required. Common products include:
- Syringes
- Medical trays
- Diagnostic instrument housings
4. Electronics
The electronics industry benefits from injection molding through components like:
- Housings for various devices
- Connectors
- Switches
Innovations in Injection Molding Technology
The world of injection molding is continually evolving with new technologies that improve efficiency, reduce costs, and enhance product quality. Some notable innovations include:
- 3D Printing for Prototyping: Rapid prototyping using 3D printing has revolutionized the design phase, allowing for faster feedback and iterations on mold designs.
- Smart Factories: With the advent of Industry 4.0, many factories are now utilizing IoT (Internet of Things) technology to monitor production processes in real-time, leading to optimization and reduced downtime.
- Advanced Materials: The development of new materials, such as bioplastics, is paving the way for more sustainable manufacturing practices.
Choosing the Right Injection Mold Factory
Selecting the right injection mold factory is a critical decision that impacts the success of your products. Here are some key factors to consider:
1. Experience and Expertise
Check the factory's history and experience in your specific industry. A company that has worked on similar projects will better understand your unique requirements.
2. Quality Assurance
Evaluate the factory’s quality control processes. A high-quality factory should have certifications such as ISO standards to ensure they meet international benchmarks.
3. Technology and Equipment
Inquire about the technology and machinery used in the manufacturing process. Modern, sophisticated equipment often leads to better efficiency and product quality.
4. Communication and Collaboration
Effective communication is key to a successful partnership. Choose a factory that values transparency and is willing to collaborate throughout the production process.
5. Cost Competitiveness
While cost should not be the only deciding factor, it is essential to obtain quotes from multiple factories and compare their offerings. Consider the value offered rather than just the price.
Environmental Considerations in Injection Molding
As sustainability becomes a pressing concern in modern manufacturing, injection mold factories are also evolving to adopt greener practices. This includes:
- Implementing recycling programs for scrap materials.
- Reducing energy consumption through smarter machinery and practices.
- Utilizing biodegradable materials in their production processes.
Conclusion
In summary, an injection mold factory is a pivotal component of the manufacturing landscape, driving innovation and efficiency across various industries. By understanding the intricacies of the injection molding process and the significant advantages it offers, businesses can make informed decisions to improve their production capabilities. As the industry continues to evolve, the future for injection molding appears bright, presenting new opportunities for growth and sustainability.