Understanding LEV Inspections in South Wales
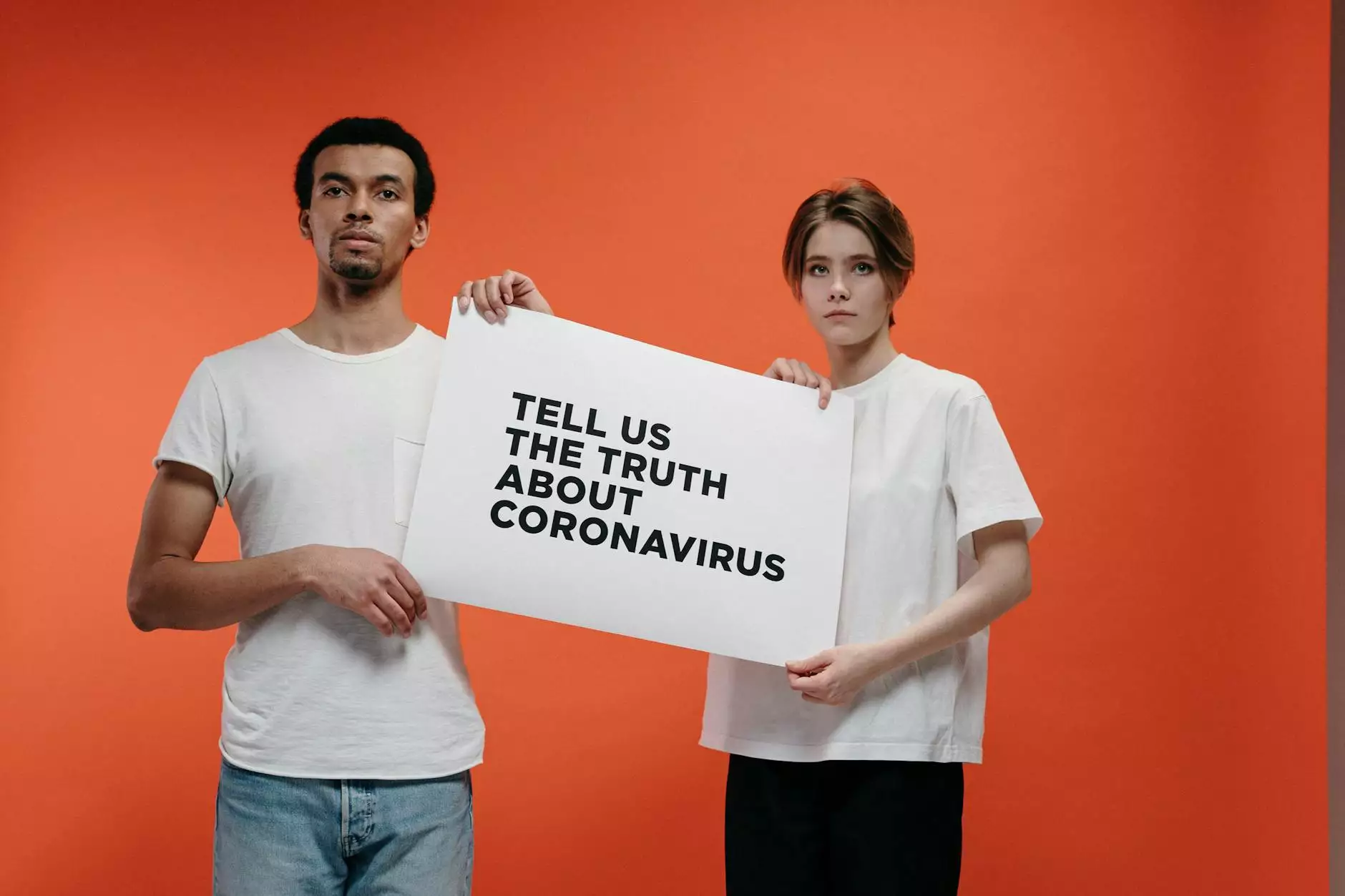
In the realm of health and safety, LEV inspection South Wales plays a critical role in ensuring that workplaces are safe for employees. Local exhaust ventilation (LEV) systems are designed to reduce employees' exposure to airborne contaminants, making regular inspections vital for compliance and safety. This article will delve into the significance of LEV inspections, the process involved, and tips for businesses in South Wales to ensure they meet regulatory standards.
What is LEV?
Local exhaust ventilation systems are a crucial part of health and safety management in industries where workers may be exposed to hazardous substances. These systems are designed to:
- Capture: They capture airborne contaminants at the source before they can disperse into the working environment.
- Filter: Filters within the system remove harmful particles, pollutants, and gases.
- Discharge: The clean air is then discharged back into the environment or safely vented outside.
Why Are LEV Inspections Important?
Regular LEV inspections in South Wales are legislated by the Control of Substances Hazardous to Health (COSHH) Regulations. The importance of these inspections can be summarized as follows:
1. Compliance with Regulations
Businesses in South Wales must adhere to strict health and safety regulations. Regular inspections ensure compliance, avoiding potential legal repercussions and penalties.
2. Protecting Employee Health
Worker safety should always be a priority. Regular inspections help maintain effective LEV systems that protect employees from exposure to harmful substances, ultimately ensuring their health and well-being.
3. Reducing Downtime and Costs
Preventive maintenance through inspections decreases the likelihood of system failures, which can lead to costly downtime for repairs and lost productivity.
How Often Should LEV Inspections Be Conducted?
According to health and safety regulations, LEV systems should be inspected:
- Annually: It is recommended to perform a thorough inspection of LEV systems at least once a year.
- After Changes: Any alterations to the system or changes in the processes should prompt an immediate inspection.
- Following Maintenance: After any maintenance work, an inspection should be conducted to ensure operational efficiency.
What Does an LEV Inspection Involve?
The LEV inspection process typically includes several critical steps to ensure the system operates effectively:
1. Visual Inspection
The inspector will start with a thorough visual examination of the entire LEV system, including:
- Hoods and capture devices
- Extract ducts
- Filters
- Fans and discharge outlets
2. Functional Testing
Next, the inspector will perform functional tests by:
- Measuring airflows at various points in the system.
- Testing for leaks in ducts and seals.
- Assessing the operating condition of fans and filters.
3. Documentation and Reporting
After the inspection, a detailed report will be generated outlining:
- The condition of the LEV system.
- Any remedial actions required.
- Recommendations for improvements or upgrades.
Choosing the Right Inspection Service
Finding a reputable LEV inspection service in South Wales is crucial for the safety of your workplace. Here are some key factors to consider:
1. Qualifications and Experience
Ensure that the inspection service has qualified professionals with experience in conducting LEV inspections. Look for certifications and accreditations relevant to health and safety.
2. Comprehensive Services
A full-service inspection should include not only assessment and testing but also maintenance and repair services, as needed. This will ensure that all your LEV system needs are met under one roof.
3. Reputation and Reviews
Research the reputation of the company through reviews and testimonials. Word-of-mouth recommendations and online reviews can offer valuable insights into the quality of service provided.
Cost of LEV Inspections in South Wales
The cost of LEV inspections can vary based on several factors, including:
- Size and complexity of the LEV system
- Location and accessibility of the system
- Additional services required, such as maintenance or repairs
Typically, businesses can expect to pay anywhere from a few hundred to several thousand pounds, depending on these factors. However, investing in regular inspections can prevent more significant costs associated with health issues or regulatory fines.
Maintaining Your LEV System
Here are some essential tips for maintaining your LEV system effectively:
1. Regular Checks
In addition to annual inspections, conduct regular checks on the system’s operation and cleanliness. This vigilance can help catch minor issues before they escalate.
2. Train Employees
Ensure that all employees are trained on the importance of the LEV system and how to report issues. Awareness can lead to quicker identification and resolution of potential problems.
3. Schedule Proactive Maintenance
Consider scheduling ongoing maintenance even beyond the annual inspections to ensure optimal performance of the LEV system.
Conclusion
In conclusion, LEV inspection South Wales is an indispensable part of workplace health and safety management. Regular inspections not only ensure compliance with legal standards but also safeguard the health of employees and the overall productivity of the business. By selecting a qualified inspection service, maintaining the LEV system, and fostering a culture of safety within the organization, businesses can significantly mitigate risks associated with hazardous airborne contaminants.
Investing in regular LEV inspections and maintenance is a proactive step that businesses in South Wales should prioritize. For quality and reliable LEV inspection services, visit Safe Plant UK today.