The Essential Role of a Plastic Mould Maker in Modern Industry
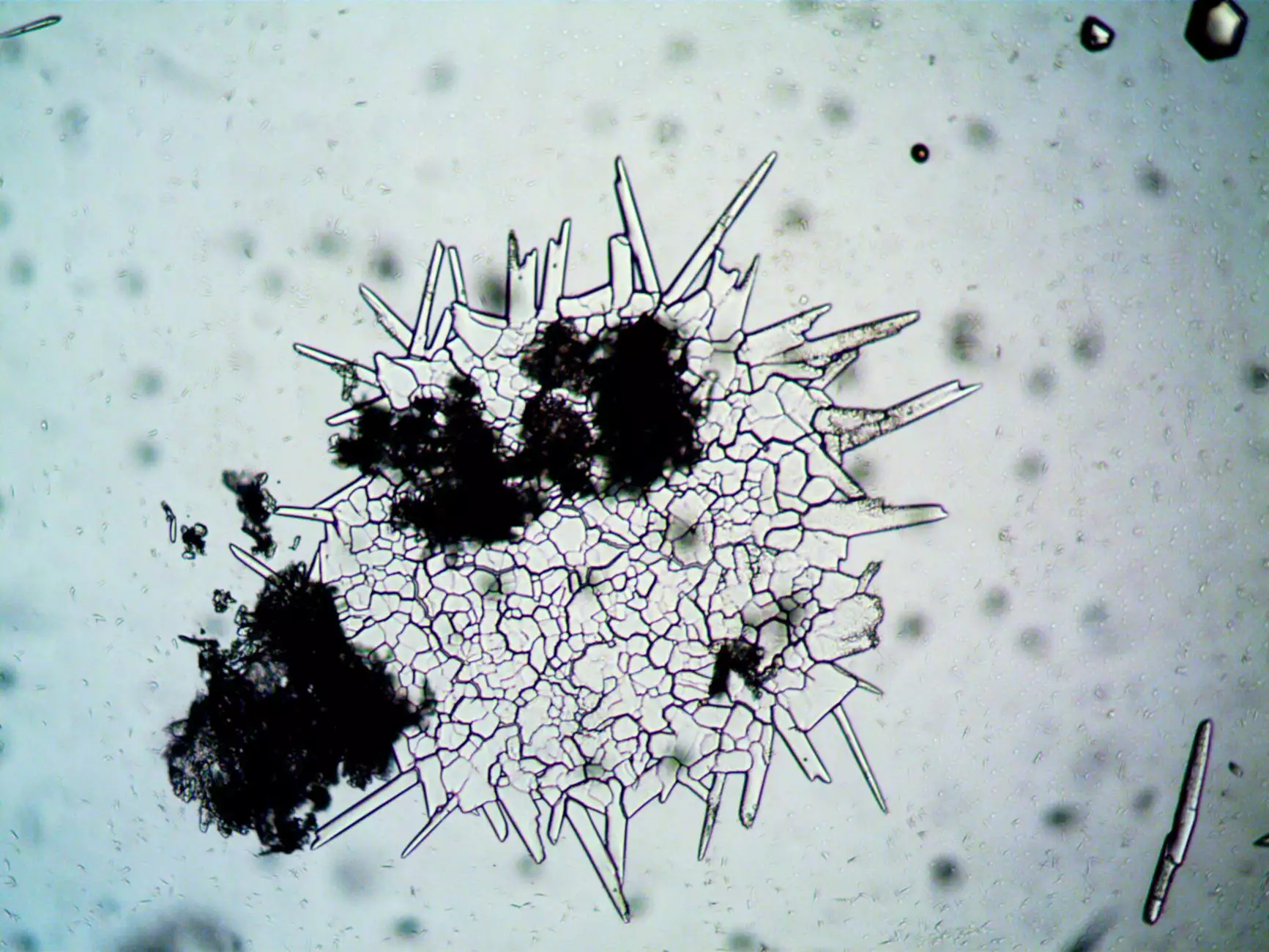
In today's fast-paced manufacturing landscape, the demand for precision and efficiency has never been higher. One of the unsung heroes of this industry is the plastic mould maker. This pivotal role contributes significantly to the production of high-quality products across various sectors.
What is a Plastic Mould Maker?
A plastic mould maker is a professional responsible for designing and fabricating moulds used in the production of plastic components. These moulds form the shape and design of the final product and are crucial for ensuring consistency and quality during mass production.
The Importance of Mould Design
Effective mould design is vital. It not only influences the quality of the final product but also affects the efficiency of the manufacturing process. Here are some key aspects of mould design:
- Precision: Accurate moulds minimize defects and ensure that products meet exact specifications.
- Material Selection: Choosing the right materials for the mould can greatly affect durability and production cost.
- Cooling Channels: Well-designed cooling systems within the mould enhance the cycle time by allowing faster cooling of the plastic.
- Ease of Maintenance: Moulds must be designed for easy access and repair to minimize downtime.
Processes Involved in Mould Making
Creating a mould involves several intricate processes, each requiring a high level of expertise. The main steps include:
1. Conceptualization and Design
The first stage in the plastic mould maker's journey is to work closely with product designers to understand the specifications and requirements of the product. This can include:
- 3D modeling and simulations
- Prototype development for testing
2. Material Selection
Choosing the right material for the mould is critical. Typical materials include:
- Steel: Known for its strength and durability.
- Aluminum: Preferred for prototyping due to its lighter weight and ease of machining.
- Bronze: Used in more specialized applications for its wear resistance.
3. Machining the Mould
Once the design is finalized and materials selected, the next step involves machining the mould using CNC machines, EDM (Electrical Discharge Machining), and traditional machining techniques. This stage requires a profound understanding of tool paths and tolerances to ensure precision.
4. Assembly and Testing
After machining, the mould components must be assembled. Testing the mould in various conditions is imperative to check for any inconsistencies. This phase may include:
- Trial runs with the chosen plastic material
- Adjustments and fine-tuning based on performance
Benefits of Employing a Skilled Plastic Mould Maker
Investing in a highly skilled plastic mould maker can result in numerous advantages for manufacturing companies. These benefits include:
- Increased Efficiency: High-quality moulds lead to quicker production cycles.
- Cost-Effectiveness: Well-designed moulds reduce scrap and rework, cutting costs.
- Enhanced Product Quality: Precision in mould making ensures higher-quality end products, reducing returns and complaints.
- Innovation: Skilled mould makers can contribute innovative ideas and techniques that enhance product development.
Case Studies: Success Stories of Mould Craftsmanship
To understand the impact of professional plastic mould makers, let's explore a few hypothetical case studies where their expertise has made a clear difference:
Case Study 1: Automotive Industry
In the automotive industry, a leading manufacturer faced challenges with high failure rates in plastic components for vehicles. By collaborating with experienced plastic mould makers, they redesigned their moulds and implemented better cooling systems. This resulted in:
- Hovering production costs by 20%
- A significant reduction in defects, resulting in improved safety ratings
Case Study 2: Consumer Goods Sector
A company specializing in consumer goods sought to introduce a new line of eco-friendly products. By employing advanced mould-making techniques, they were able to:
- Optimize the use of bioplastics while maintaining structural integrity
- Speed up their time to market by 15% with the introduction of lean manufacturing practices in mould production
Future Trends in Plastic Mould Making
As the manufacturing environment continues to evolve, so too do the methodologies employed by plastic mould makers. Here are some notable trends:
- Adoption of 3D Printing: This technology offers the ability to produce complex parts with less material waste.
- Sustainability: With stricter regulations on plastic use, mould makers are increasingly focusing on sustainable practices.
- Smart Manufacturing: Integrating IoT devices to monitor mould conditions in real-time can enhance productivity.
Choosing The Right Plastic Mould Maker
Finding the right plastic mould maker is critical for any manufacturing business aiming for success. Here are some key factors to consider:
- Experience: Look for a professional with a strong portfolio in your specific industry.
- Technical Skills: Ensure they are well-versed in the latest technologies.
- Reputation: Research their reputation through customer reviews and testimonials.
- Support Services: Consider whether they offer post-production support and maintenance services.
Conclusion: Investing In The Future of Manufacturing
Ultimately, the role of a plastic mould maker is critical to the success of various industries. Their ability to innovate, optimize, and create high-quality moulds lays the foundation for efficient manufacturing processes and quality products that meet the demands of today’s consumers.
At Deep Mould, we pride ourselves on our experience and commitment to excellence in mould making. Understanding the intricacies of mould production not only helps us improve our services but also empowers our clients to achieve their manufacturing goals. With an emphasis on quality, sustainability, and technological advancement, the future of mould making is bright, and we are excited to lead the way.