Understanding Precision Plastic Injection Molding
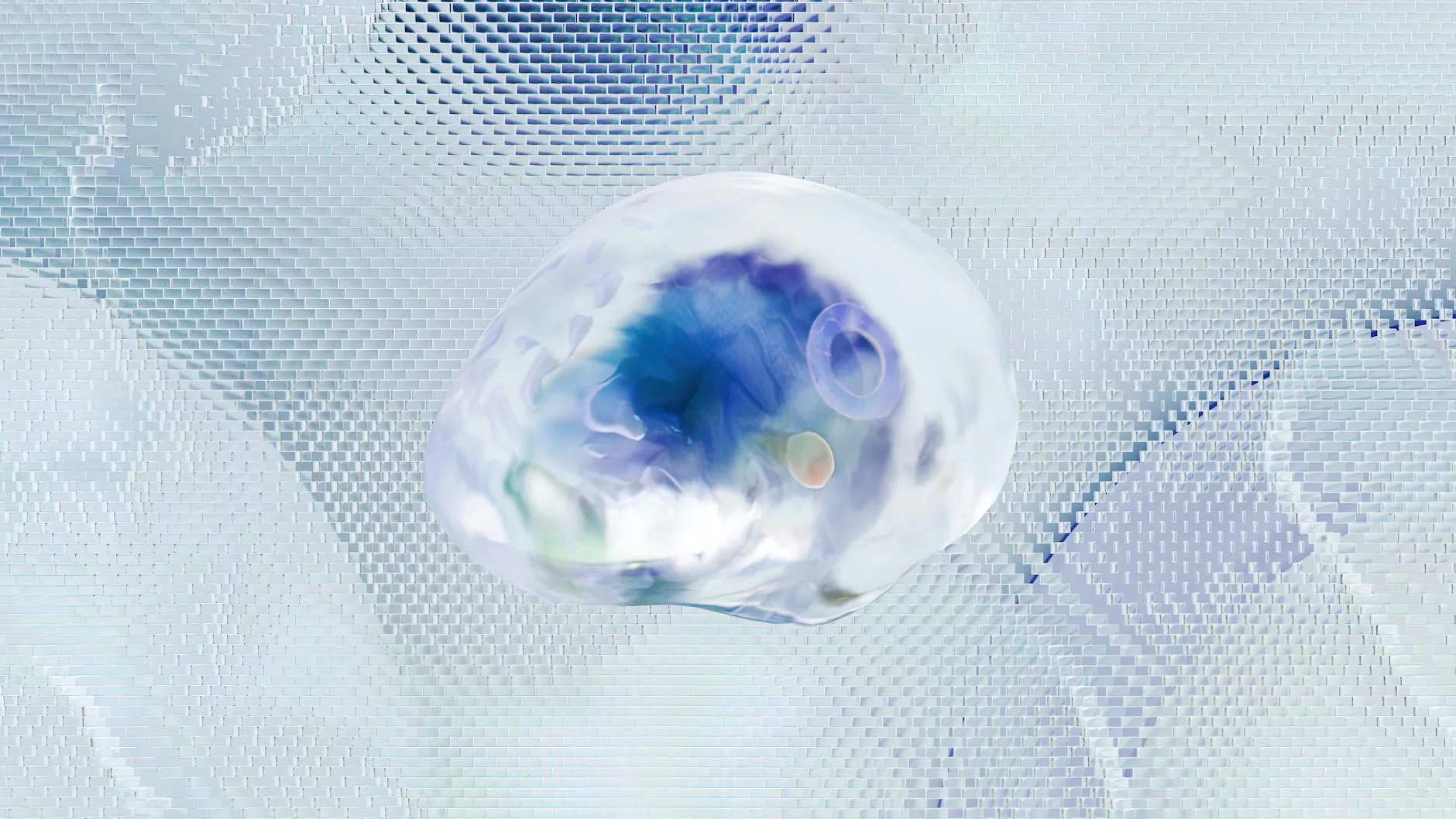
In the dynamic landscape of modern manufacturing, the term precision plastic injection molding has become synonymous with high-quality production and innovative design. This sophisticated process allows manufacturers to produce intricate plastic components with unrivaled accuracy and efficiency. We delve into the intricacies of this technology, its benefits, and its applications in various industries, particularly in metal fabrication.
What is Precision Plastic Injection Molding?
At its core, precision plastic injection molding is a manufacturing process through which plastic materials are melted and injected into a mold cavity under high pressure. The process can produce highly detailed parts, enabling manufacturers to achieve exceptional tolerances and surface finishes. Key characteristics of this process include:
- High Speed: The process allows for rapid production cycles, which are crucial for meeting market demands.
- Cost-Effectiveness: Although the initial setup can be costly, mass production significantly reduces per-unit costs.
- Versatility: A variety of plastic resins can be used, making this method suitable for diverse applications.
The Technology Behind Precision Plastic Injection Molding
The technology that underpins precision plastic injection molding is remarkable. It involves several key stages:
- Material Preparation: Plastic pellets are fed into a heated barrel where they are melted down to a viscous form.
- Injection: The molten plastic is injected into a mold at high pressure, allowing it to conform to detailed shapes.
- Cooling: The plastic part is allowed to cool and solidify within the mold.
- Ejection: Once cooled, the mold opens, and the finished part is ejected.
- Post-Processing: After ejection, additional steps such as trimming or painting may take place.
Benefits of Precision Plastic Injection Molding
The advantages of adopting precision plastic injection molding in manufacturing processes are profound. Here are some of the most significant benefits:
- Enhanced Product Accuracy: High precision leads to lower tolerances, ensuring parts fit together flawlessly.
- Reduced Waste: The process minimizes excess material, leading to more sustainable operations.
- Scalability: Ideal for both low and high-volume production runs, this process can grow with your business needs.
- Improved Surface Finish: The injection molding process can produce smooth surfaces which often require little to no further finishing.
- Design Flexibility: Complex shapes that would be challenging to create using other methods can be achieved easily.
Applications in Metal Fabrication
In the realm of metal fabricators, the intersection of metal and plastic has given rise to innovative hybrid products. Although traditionally seen as separate categories, precision plastic injection molding can significantly enhance metal fabrication processes in several ways:
Combining Strength with Lightweight Design
Many industries, including automotive and aerospace, require components that are both strong and lightweight. By using precision plastic injection molding, manufacturers can create intricate plastic parts that complement metal structures, reducing overall weight without compromising strength.
Seamless Integrations of Plastic Parts in Metal Components
With the capability of creating tight tolerances, precision plastic injection molding allows for plastic parts to integrate seamlessly with metal components, reducing the need for extensive assembly work and enhancing overall structural integrity.
Simplifying Complex Assemblies
The ability to produce multi-functional parts means that manufacturers can combine multiple components into a single plastic part, simplifying assembly and thereby enhancing efficiency. This leads to significant reductions in assembly time and labor costs.
Choosing the Right Partner for Precision Plastic Injection Molding
When looking for a manufacturing partner specializing in precision plastic injection molding, several factors should come into play:
- Experience: Check the partner’s industry experience and past projects to ensure they can meet your specific needs.
- Technology: Ensure they use the latest equipment and technology for optimal production efficiency and precision.
- Quality Assurance: Robust quality control processes are essential to ensure that all parts meet established specifications.
- Customization Capabilities: Your partner should be able to tailor solutions to fit your unique requirements.
- Customer Support: Access to knowledgeable representatives and responsive support can significantly enhance collaboration.
The Future of Precision Plastic Injection Molding
The future of precision plastic injection molding is promising, with several trends shaping its evolution:
- Sustainable Practices: There is an increasing demand for eco-friendly materials and processes that minimize environmental impact.
- Smart Manufacturing: The integration of IoT technology to monitor and optimize production processes is on the rise.
- Advanced Materials: Development of new types of plastics capable of withstanding higher temperatures and providing better performance.
- 3D Printing Synergy: The combination of traditional molding and additive manufacturing is opening new avenues for product development.
Conclusion
In conclusion, precision plastic injection molding is no longer just a method of producing parts; it is a critical component of modern manufacturing and metal fabrication. Its ability to deliver high-quality, precise components at scale empowers industries to innovate and create complex products that meet today’s demanding market. As the industry continues to evolve, businesses that embrace this advanced manufacturing technique are poised to achieve remarkable growth and success.
For the best in precision plastic injection molding, considering partners like Deep Mould can set your business on the path for enhanced performance and competitive advantage.