Unleashing Innovation with Premier Prototype Mold Manufacturers in Metal Fabrication
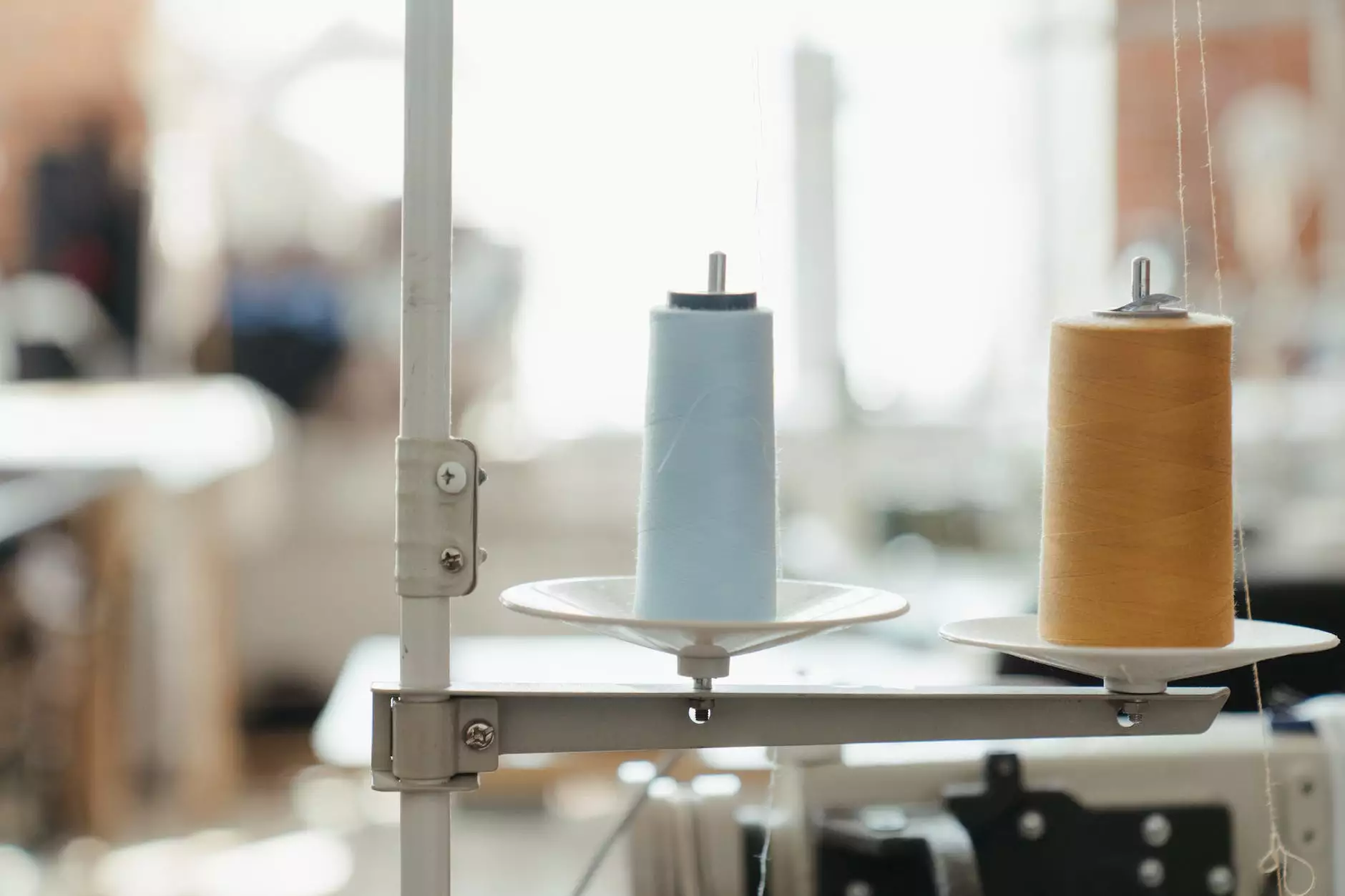
In the fast-paced world of industrial manufacturing, prototype mold manufacturers play a crucial role in transforming conceptual designs into tangible, functional products. These specialized companies are the backbone of innovation, enabling industries to test, validate, and refine their ideas with precision and efficiency. As businesses strive to bring high-quality metal components to market faster than ever before, the importance of partnering with the right prototype mold manufacturers cannot be overstated.
What are Prototype Mold Manufacturers and Why Do They Matter?
Prototype mold manufacturers are specialized entities that design, engineer, and produce prototypes of molds used in the manufacturing of metal parts. Unlike mass production molds, prototypes focus on creating functional models that allow companies to evaluate design, performance, and manufacturability before scaling up to full production. This process significantly reduces risks, cuts costs, and accelerates product development timelines.
The Significance of High-Quality Prototype Molds in Modern Industry
In the realm of metal fabrication, the quality of the prototype mold directly influences the final product outcome. Here’s why the expertise of top prototype mold manufacturers impacts your business:
- Precision and Accuracy: High-quality molds ensure dimensional accuracy, essential for fit and function in complex assemblies.
- Material Compatibility: Expert manufacturers select optimal materials for mold durability and performance with various metals and alloys.
- Cost-Effectiveness: Accurate prototypes minimize the need for multiple revisions, saving both time and money.
- Faster Time-to-Market: Efficient mold creation accelerates the testing and validation process, allowing businesses to launch products swiftly.
- Design Flexibility: Advanced prototype molds accommodate intricate geometries and innovative features.
Key Factors to Consider When Choosing a Prototype Mold Manufacturer
Partnering with the right prototype mold manufacturer is critical for project success. Here are essential criteria to evaluate:
- Material Capabilities: Manufacturers should work with a wide range of materials suitable for various metals and applications.
- Technological Expertise: Look for companies utilizing state-of-the-art equipment such as CNC machining, EDM, and 3D printing.
- Design Support: A reliable manufacturer offers comprehensive design assistance to optimize mold performance and manufacturability.
- Quality Assurance: Certifications like ISO 9001 ensure consistent quality standards and process reliability.
- Lead Time and Flexibility: Quick turnaround times and adaptability to project changes are vital for dynamic industries.
- Reputation and Past Projects: Reviewing case studies and client testimonials indicates their capacity for complex and high-precision mold fabrication.
The Manufacturing Processes of Leading Prototype Mold Manufacturers
Effective prototype mold manufacturers utilize a blend of advanced manufacturing processes to produce high-quality prototypes. Understanding these methods can shed light on their capabilities:
- CNC Machining: Computer-controlled cutting tools produce precise molds from metal blocks, suitable for complex geometries with tight tolerances.
- Electrical Discharge Machining (EDM): Used for intricate details and difficult-to-machine features, EDM provides exceptional precision.
- 3D Printing and Additive Manufacturing: Ideal for rapid prototyping and complex internal features, enabling quick iterations.
- Surface Treatment and Finishing: Processes such as polishing, coating, and heat treatment enhance mold surface quality and durability.
Advantages of Partnering with DeepMould.net — A Top Prototype Mold Manufacturer in Metal Fabrication
At DeepMould.net, we pride ourselves on offering comprehensive solutions in metal fabrication with a specialization as prototype mold manufacturers. Here’s what distinguishes us:
- Unmatched Precision: We utilize cutting-edge CNC and EDM technologies to ensure each mold meets exact specifications.
- Extensive Material Expertise: Our team is proficient in working with a wide range of metals including aluminum, brass, steel, and exotic alloys.
- Design Optimization: We collaborate closely with clients from the initial concept to refine the design for manufacturability and longevity.
- Rapid Turnaround: Our efficient processes enable fast production without compromising quality, reducing your time-to-market.
- Comprehensive Quality Control: Every mold undergoes rigorous testing and inspection to ensure standards are exceeded.
- Global Reach and Support: Our expansive network allows us to serve international clients with consistent excellence.
Case Studies Showcasing Excellence in Prototype Mold Manufacturing
DeepMould.net has successfully completed numerous projects across diverse industries, including automotive, aerospace, electronics, and consumer goods. These case studies highlight our commitment to quality and innovation:
Automotive Industry: High-Precision Prototype Molds for Engine Components
We provided bespoke prototype molds for complex engine parts, ensuring high accuracy and surface finish, enabling our client to conduct rigorous testing before launching mass production.
Electronics Sector: Miniature Molds for Connectors
Our team crafted intricate molds for tiny electronic connectors, demonstrating our capability to produce detailed features within strict tolerances.
Aerospace Applications: Durable Molds for Mechanical Parts
Our durable molds with high thermal stability allowed aerospace manufacturers to create components that endure extreme conditions.
Future Trends in Prototype Mold Manufacturing and Metal Fabrication
The industry is evolving rapidly with advancements that promise greater efficiency and innovation. Here are some emerging trends:
- Smart Manufacturing: Integration of IoT and automation for real-time monitoring and process optimization.
- Additive Manufacturing Expansion: Increased use of 3D printing for rapid iterations and complex geometries.
- Advanced Materials: Development of novel alloys and composites for enhanced mold performance.
- Sustainable Practices: Adoption of eco-friendly processes to reduce waste and energy consumption.
- Enhanced Design Software: Use of AI-driven CAD tools for optimized mold design and simulation.
Choosing the Right Prototype Mold Manufacturer for Your Business Growth
Partnering with a proven prototype mold manufacturer like DeepMould.net ensures your product development process is robust, flexible, and innovative. Here are steps to select the best partner:
- Assess their technological capabilities and equipment.
- Review their experience in your industry and project types.
- Verify quality certifications and compliance standards.
- Evaluate their communication, support, and adaptability.
- Request quotes and lead times to compare value propositions.
Conclusion: Elevate Your Metal Fabrication with Superior Prototype Mold Solutions
In conclusion, the success of any metal fabrication project hinges on the quality and precision of the prototype molds used in preliminary stages. The leading prototype mold manufacturers — exemplified by DeepMould.net — combine cutting-edge technology, extensive industry expertise, and a customer-centric approach to deliver molds that meet the highest standards of quality and efficiency.
By choosing the right partner, your business gains a competitive edge, reduces development risks, and accelerates time-to-market. Embrace the future of metal fabrication with innovative prototype solutions that lay the foundation for exceptional products and sustained growth.